
Using SCP Technology in Concrete Repair for Chloride Mitigation
Concrete is the most common building material used today, utilized two times more than all other building materials combined. Since the late-1800’s, the use of reinforced concrete has been the most widely used concrete construction practice globally because the reinforcement helps concrete in tension. This use of reinforced concrete has allowed mankind to build bigger, taller, and more unique structures. Giving mankind the ability and opportunity to create and imagine buildings that have not been able to come to fruition. One issue of reinforced concrete is the durability and longevity due to the corrosion potential of the reinforcement. Reinforcing steel corrosion is the number one cause of failure in reinforced concrete structures.
Corrosion, as defined by American Concrete Institute (ACI), is the deterioration of a material, usually a metal, that results from a chemical reaction with its environmenti. The corrosion of reinforcing steel is an electrochemical reaction consisting of the flow of electrons and ions that produces a deterioration of the steel and its properties. One significant way to reduce the corrosion potential is to completely encapsulate reinforcing steel in concrete with a high pH value, as the high alkaline environment acts as a protective oxide film. If no other outside forces are applied to the reinforced concrete, the steel should not rust. Unfortunately, almost all reinforced concrete is exposed to environmental conditions that shorten its lifespan, increasing the potential for corrosion.
The corrosion potential of reinforcing steel is influenced by several factors: moisture intrusion, lowered pH values over time, quality of the concrete and construction materials, proper concrete coverage of reinforcing steel, initial curing conditions and the formation of cracks in the concrete. These factors can speed up chloride movement into the concrete, disrupting the protective oxide film around the reinforcing steel which leads to rusting. Chlorides are important when examining reinforcing steel corrosion in concrete because they breach the passive layer around the rebar. The passive layer around rebar is a film created by the high pH (alkalinity) of concrete through which oxygen cannot penetrate. A prevailing theory is that chloride ions increase the solubility of the passive layer, causing it to give way at a threshold concentration ii. Once the passive layer is penetrated, the corrosion action no longer needs chlorides to progress, and is typically self-sustaining, needing only the rebar, water, and oxygen to progress. The primary consideration after the passive layer is breached by chlorides then becomes the pore structure of the concrete along with the electrical resistivity that the pore structure provides. iii
Once the protective layer has been interrupted by chlorides or other sources, the corrosion reaction becomes self-sustaining and only requires the presence of water and oxygen. This corrosion can lead to spalling and delamination of the concrete structure and reduced tensile capacity.
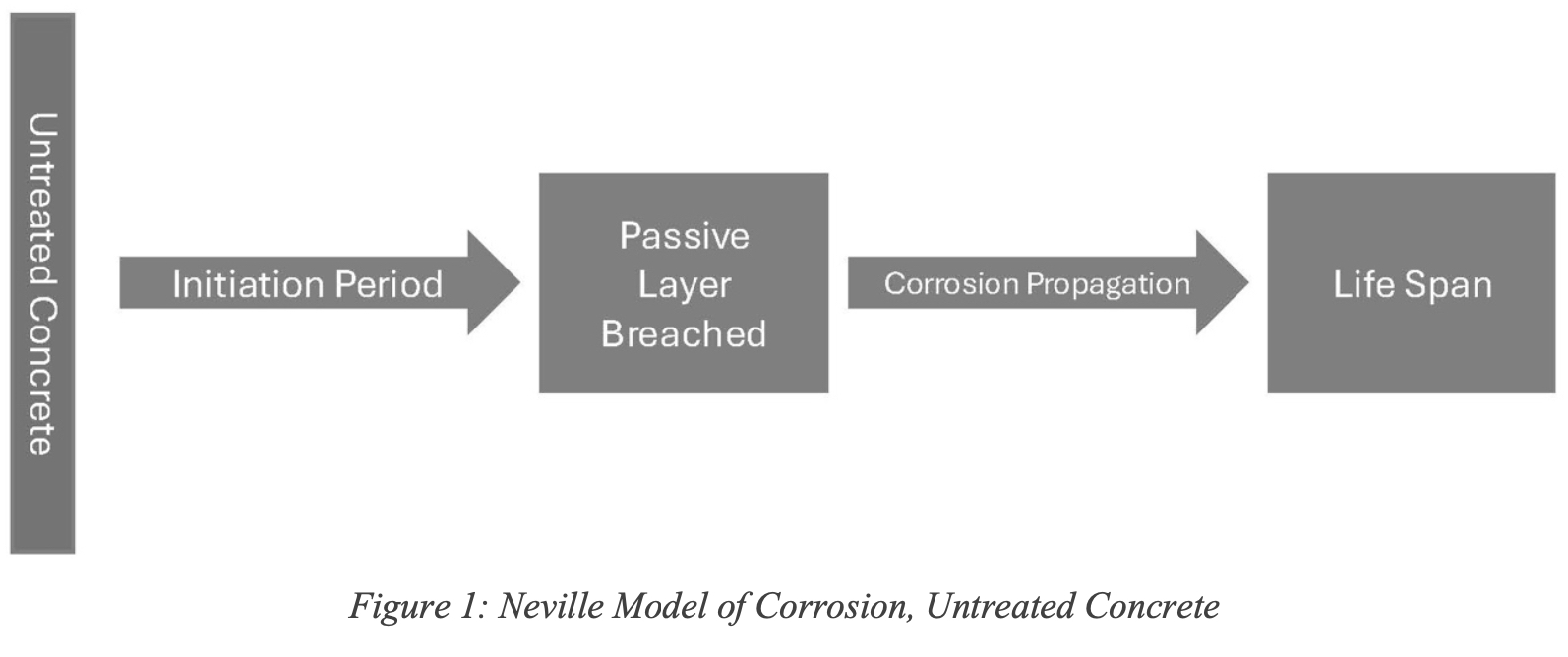
How Spray-Lock Concrete Protection Products Work
SCP technology works by penetrating deeply into the concrete substrate and filling the accessible capillary and pore structure. This filling of void space is achieved when available alkalis present in the concrete come in contact and react with the silica particles in SCP products. The product of the reaction that fills the void spaces is primarily calcium silicate hydrate (C-S-H), the main product of Portland cement hydration reaction. The reaction takes place internally. SCP products do not form a membrane that is left on the surface. Like the C-S-H formation from the cement hydration process, the SCP reaction products are a permanent part of the concrete in the interaction zone. By filling these spaces, SCP products waterproof concrete within the interaction zone. If the concrete structure does not have any structural cracks, SCP products also waterproof the structure in the application area, even under hydrostatic pressure. With SCP treatments preventing moisture migration from carrying chlorides within the concrete matrix and restricting external sources of water reaching the reinforcing steel, the corrosion potential is greatly reduced.
The application is a one-time treatment unlike other topical concrete treatments, such as acrylics, epoxies, and polyurethanes. SCP is a penetrating concrete treatment that does not change the surface of the concrete. An SCP application is not a coating and has no negative effect on bond integrity.
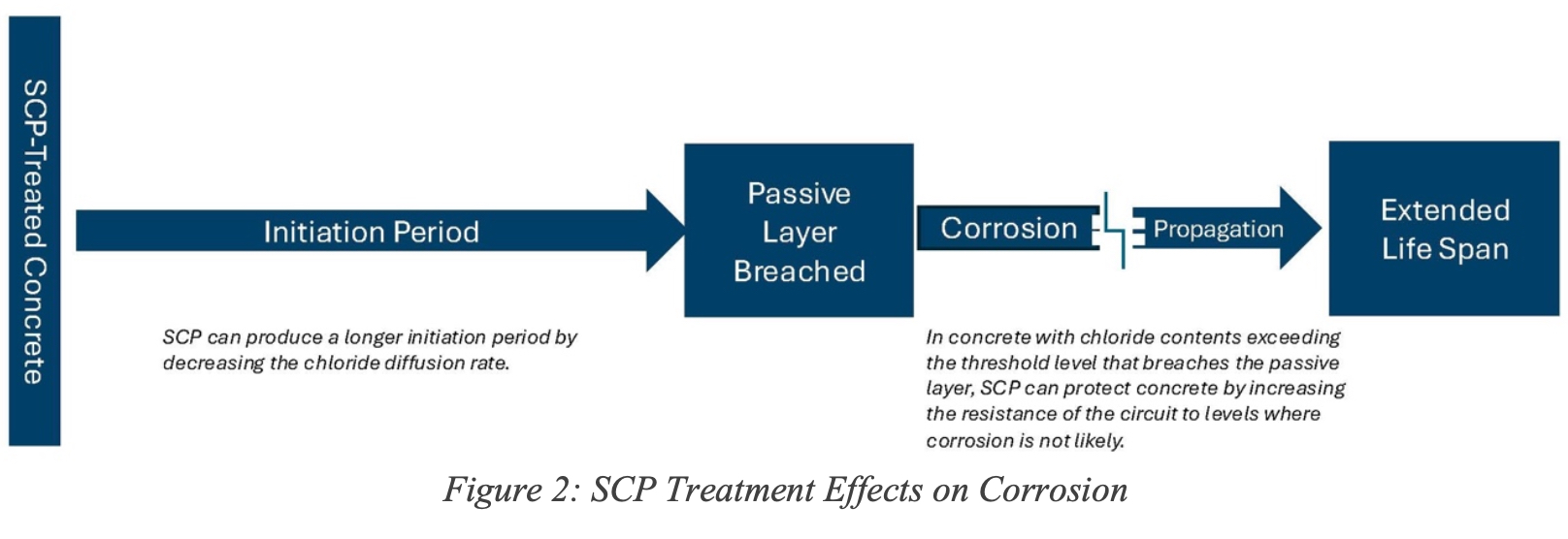
Chloride bulk diffusion involves ponding salt water on top of concrete and testing the chloride concentrations at various depths according to AASHTO T-259 or ASTM C1556. This information can then be input into calculations to produce an average diffusion coefficient (D) that can be utilized to predict the amount of time that it will take for chlorides to reach reinforcing steel and penetrate the passivation layer around it. These predictions are modeled with software such as Life 365. When the diffusion coefficient is reduced, the time needed for chlorides to reach and penetrate the passive layer is extended thereby extending a structure’s life expectancy. Laboratories have tested SCP’s performance in chloride bulk diffusion situations in conventional concrete. The results of these tests are presented below.
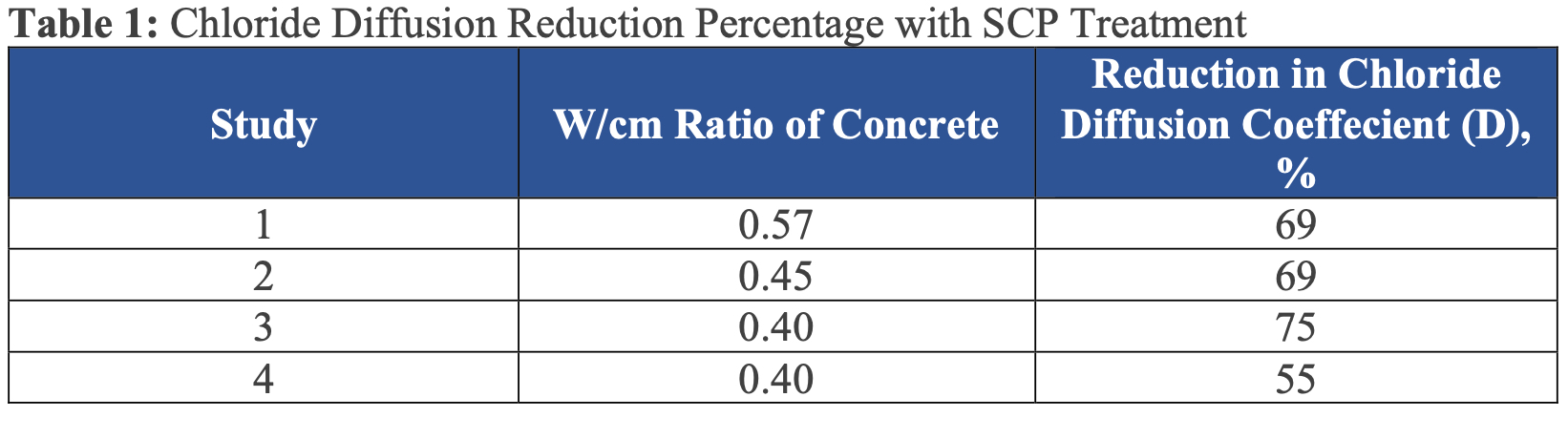
To summarize, the reduction in chloride diffusion rate provided by SCP treatments has the potential to add years of time in the field before chlorides reach reinforcing steel.
Existing Reinforced Concrete Repair Strategy with SCP Products
When reinforcing steel corrodes, the rusting and formation of oxides causes expansion. This expansion can cause delamination of the cover concrete from the rebar. Once the concrete breaks away from the reinforcing steel, the area is open to the elements which allows for additional contamination of the concrete and further corrosion of the reinforcement. There are ways to mitigate this in existing concrete:
- Step 1: Locate any concrete delamination by tapping, chain drag, or ultrasonic methods.
- Step 2: Remove any loose concrete to below the rebar, enough to access the backside of the reinforcement so that the concrete can be prepped as described by engineer’s recommendations.
- Step 3: Clean the substrate concrete by pressure washing or blown out with pneumatic air without removing the rust layer from the reinforcing steel.
- Step 4: Treat the concrete substrate with the appropriate SCP product.
- Step 5: Clean the reinforcing steel and repair to the engineer of record’s satisfaction.
- Step 6: Use cementitious patching compound to restore the cover concrete Be sure to follow the patch material manufacturer’s recommendations for surface condition and bonding.
- Step 7: Treat the concrete patch and all surrounding concrete with the appropriate SCP product. This treatment will decrease the permeability of the patch and substrate concrete reducing the chances of the concrete repair experiencing anodic ring phenomenon – the halo effect.
Note: Cleaning of the concrete is necessary after treating with SCP and before installing patching or coating materials.
SCP Product Selection:
P3 Marine is recommended for use with most chloride-compromised concrete.
Specifying SCP Products:
Guide specifications and complete submittal packages are available for download on SCP’s website at www.concreteprotection.com. SCP’s Technical Service Team is available to assist at SCPTech@concreteprotection.com
Quality Control Methods and Field Examples:
Below is a list of QC methods to evaluate the effectiveness of SCP treatment. Each method requires testing before and after treatment with SCP products. Wait at least 14 days after SCP treatment to perform tests on the treated areas. SCP recommends performing these tests ahead of the concrete repair project in an area at least 10 ft. x 10 ft. (3 m x 3 m). Concrete and exposure conditions are highly variable. This test area will provide the Engineer of Record the information needed before undertaking the repair project.
• Core drilling (ASTM C42, BS EN 12504-1, CSA A23.1, SABS 865:1994) to perform total acid-soluble chloride content (ASTM C1152, EN 12620, CSA A23.1-09, SANS 51008) and water-soluble chloride content (ASTM C1218, EN 12620, CSA A23.1-14, SANS 3001-CO3-1, 2, 3). In general, the expectation is that the total acid-soluble chloride and water-soluble chloride results will be reduced by at least 20%.
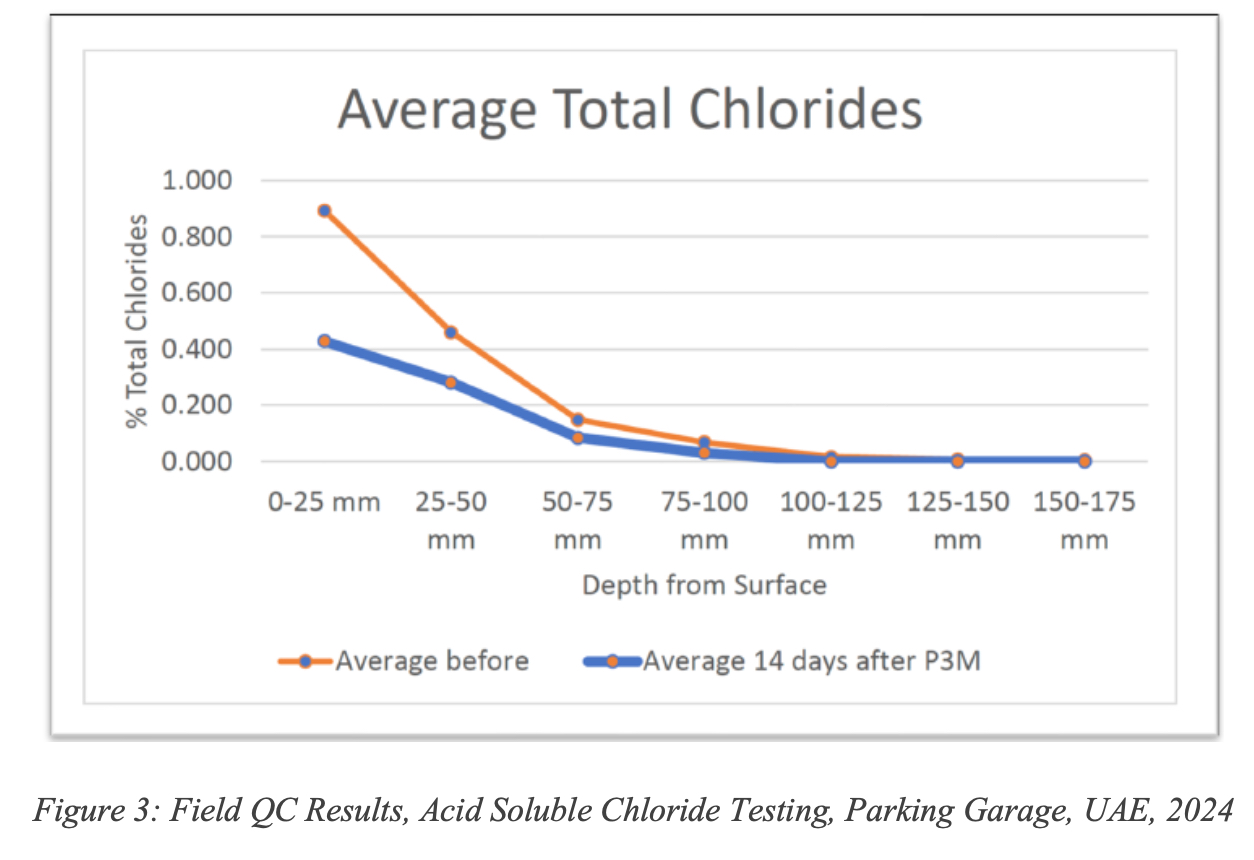
• Half-cell corrosion potentials (ASTM C876, RILEM TC 154-EMC). Treatment with SCP products should demonstrate at least a 20% improvement in half-cell corrosion potential results but can often be more significant. Be sure to include resistivity measurements when performing half-cell corrosion potentials.
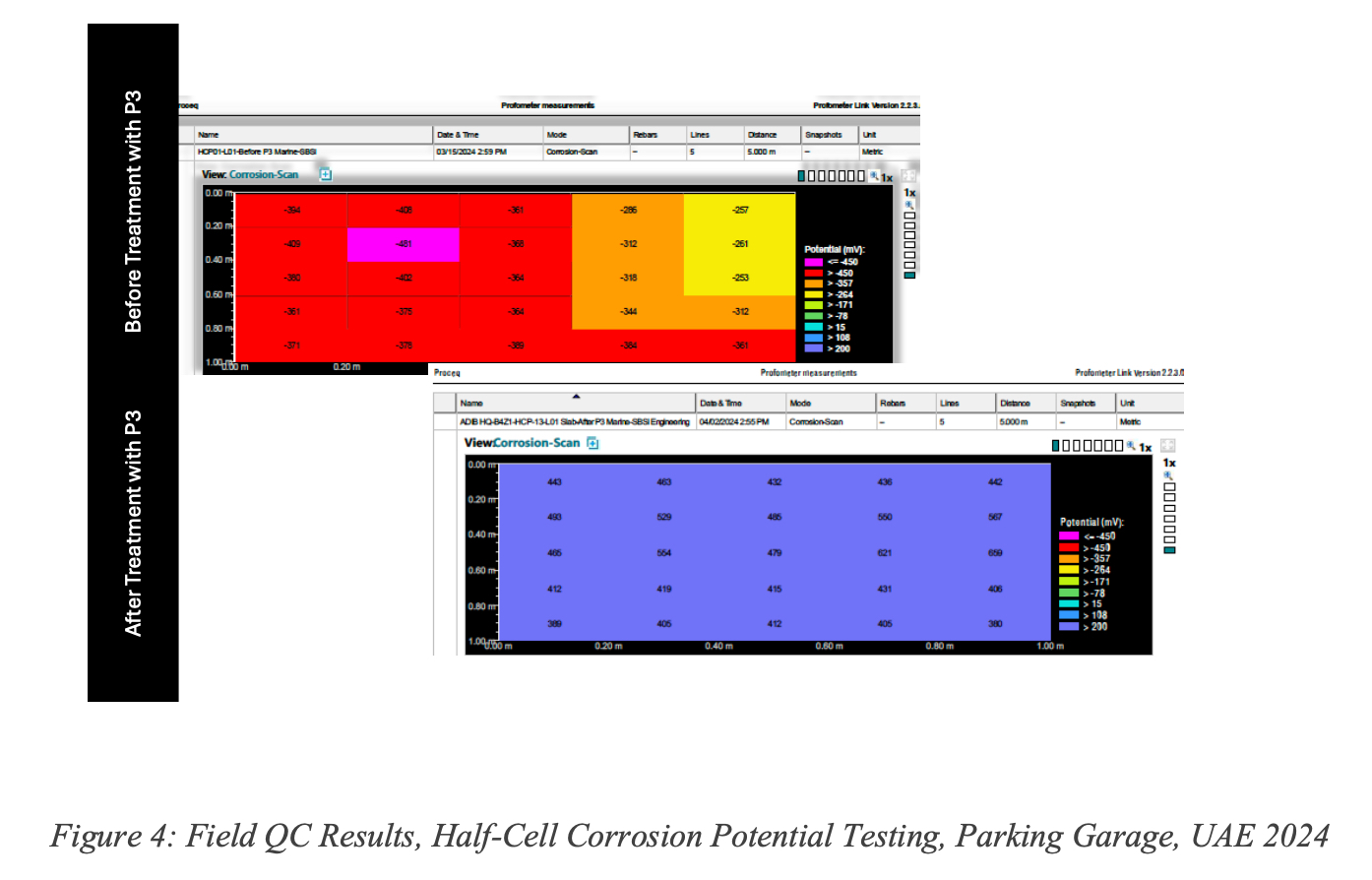
• Surface resistivity with a 4-point Wenner probe. In general, at least a 20% improvement in surface resistivity values is expected.
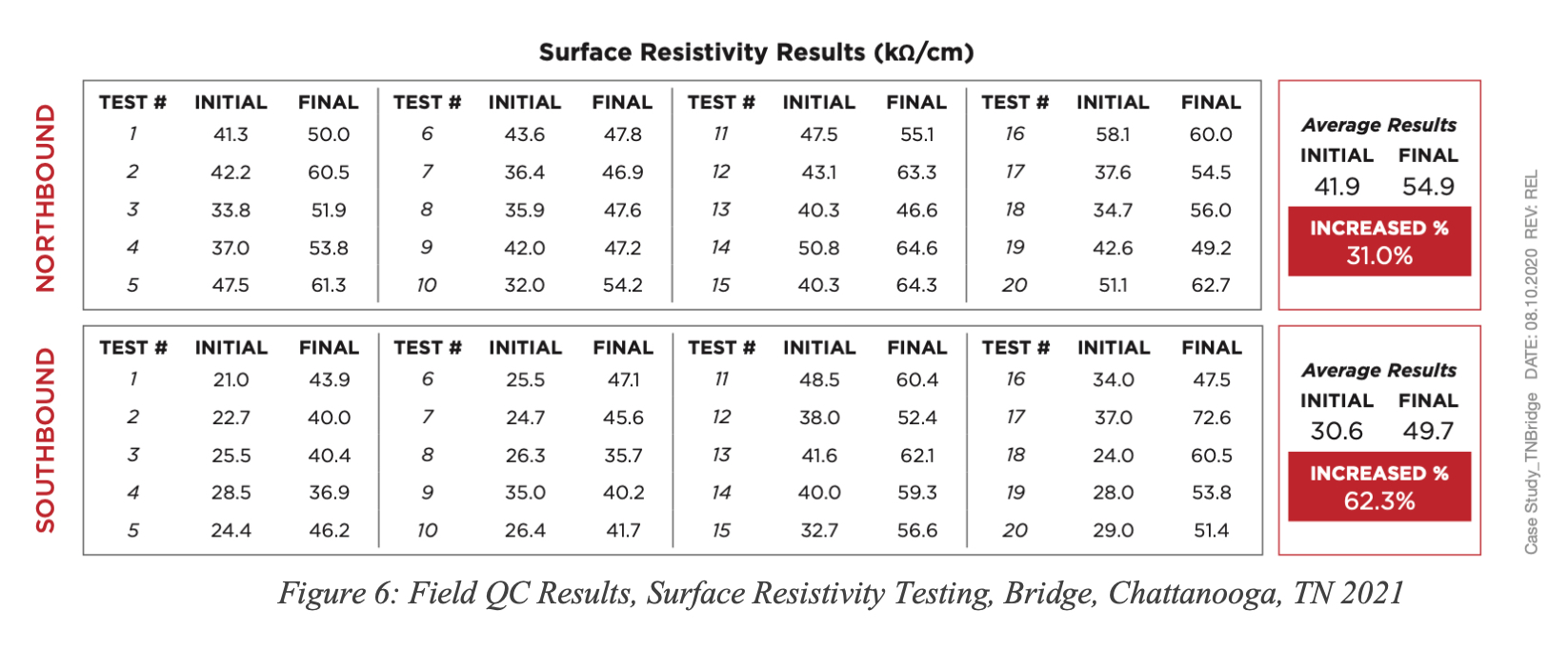
i ACI CT-13 (2013) ACI Concrete Terminology. American Concrete Institute. Farmington Hills, MI. www.concrete.org.
iiHussain, R.R. (2014) “Passive Layer Development and Corrosion of Steel in Concrete at the Nano-scale”. Journal of Civil & Environmental Engineering 4:e116
iiiNeville, Adam (1995) “Chloride Attack of Reinforced Concrete: An Overview.” Materials and Structures 28, 63-70.